сайт майстра виробничого навчання ЧОРНОКУРА Івана Валентиновича
майстер в/н
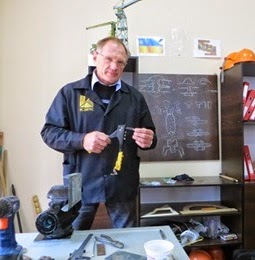
ПЛАН УРОКУ 12
Спеціальність: «Слюсар з ремонту колісних транспортних засобів»
Тема програми: СРКТЗ-3.1 « Виконання технічного обслуговування вантажних автомобілів в т.ч. спеціальних, газобалонних та дизельних ,легкових автомобілів, мікроавтобусів і автобусів ».
Тема уроку: «Технічне обслуговування коробки переключення передач. . Дослідження стану коробки передач . Ремонт коробки передач. Відновлення деталей коробки передач. Збирання та обкатка коробки передач.
Мета уроку:
навчальна: навчити здобувачів освіти володіння прийомам ремонту коробок передач, користування необхідним інструментом при відпрацьовуванні прийомів робіт з дотримання вимог ОП;
виховна: звернути увагу на раціональне використання матеріалів, економне використання енергоресурсів, бережне ставлення до обладнання та інструменту, формувати культуру виробничої діяльності;
розвивальна: формувати самостійність при виконанні робіт, сприяти розвитку технічного мислення та культури праці.
Тип уроку: Урок формування вмінь та навичок.
Вид уроку: Виконання вправ.
Матеріально – технічне забезпечення:
- інструкційно - технологічні картки;
- презентація;
- плакати по темі уроку;
- планшет з інструментами;
- компютер.
Міжпредметні зв’язки: «Спецтехнологія», «Слюсарна справа», «Охорона праці».
Література: Лудченко О. Л. "Технічне обслуговування і ремонт автомобілів”
ХІД УРОКУ
І. Організаційна частина (– 5хв).
- привітання.
- перевірка наявності здобувачів освіти.
- перевірка готовності здобувачів освіти до уроку.
- дотримання правил з охорони праці.
ІІ. Вступний інструктаж (– 40хв)
Повідомлення теми програми і уроку.
Актуалізація знань здобувачів освіти (пригадуємо пройдений матеріал)
При діагностиці та ремонті МКПП ми перевіряємо:
цілісність корпусу;
наявність патьоків трансмісійної олії;
наявність сторонніх шумів у коробці;
рівень олії;
працездатність підшипників як основних, так і голчастих;
вироблення осі та шестерень сателітів
стан синхронізаторів та вилок вибору передач;
шестерні та вали;
герметичність та знесення сальників.

ПЛАН УРОКУ 13
Спеціальність: «Слюсар з ремонту колісних транспортних засобів»
Тема програми: СРКТЗ-3.1 « Виконання технічного обслуговування вантажних автомобілів в т.ч. спеціальних, газобалонних та дизельних ,легкових автомобілів, мікроавтобусів і автобусів ».
Тема уроку: «Технічне обслуговування карданних передач. Дослідження стану карданних передач . Ремонт карданних передач. Балансування карданного валу.
Мета уроку:
- навчальна: навчити здобувачів освіти володіння прийомам ремонту карданних передач, користування необхідним інструментом при відпрацьовуванні прийомів робіт з дотримання вимог ОП;
- виховна: звернути увагу на раціональне використання матеріалів, економне використання енергоресурсів, бережливе ставлення до обладнання та інструменту, формувати культуру виробничої діяльності;
- розвивальна: формувати самостійність при виконанні робіт, сприяти розвитку технічного мислення та культури праці.
Тип уроку: Урок формування вмінь та навичок.
Вид уроку: Виконання вправ.
Матеріально – технічне забезпечення:
- інструкційно-технологічні картки;
- презентація;
Повідомлення теми програми і уроку.
Актуалізація знань здобувачів освіти (пригадуємо пройдений матеріал)
при випробуваннях на скручування (момент 4,6 кН-м) не повинно виникати залишкових деформацій та не повинна порушуватися якість зварювального шва;
Назвіть основні несправності карданної передачі, які потребують ремонту.
Назвіть основні етапи зняття сальників
Опишіть послідовність випресування підшипників
Назвіть основні етапи усування зносу шипів по діаметру
Опишіть послідовність роз’єднання вилки карданного шарніра
Підведення підсумків вступного інструктажу
підведення підсумків роботи, аналіз робот здобувачів освіти .
доведення типових помилок, способи їх усунення.
аналіз дотримання правил охорони праці
Повідомлення теми програми і уроку.
Актуалізація знань здобувачів освіти (пригадуємо пройдений матеріал)
у педалі гальма надто сильно збільшився робочий хід. Ця несправність свідчить, що з системи поступово йде гальмівна рідина. Причиною витоку зазвичай є порваний гальмівний шланг. Але іноді проблема може виникати і через гідравлічні циліндри, прокладки в яких з часом втрачають герметичність. Крім того, педаль може почати бовтатися і через повітря, що проникло в систему гальмування. Вирішення всіх цих проблем очевидне: треба переконатися, що всі елементи системи герметичні і витоків рідини ніде немає. Огляд слід розпочати зі шлангів, поступово переміщаючись до циліндрів. Підтікаючі деталі слід терміново змінити. Їзда з несправними гальмами категорично неприпустима;
Тріщин на гальмівному шлангу цілком достатньо для того, щоб водій опинився в небезпеці
автомобіль став гірше гальмувати. У якийсь момент водій ВАЗ 2106 починає помічати, що гальма схоплюються не так надійно, як раніше. Найчастіше це відбувається через те, що колодки сильно забруднились. Якщо колодки на «шістці» довго не міняти, то вони покриваються шаром олії і диск у них починає прослизати. Ще ефективність гальм може знизитися через те, що поршні в гідравлічних циліндрах втратили колишню рухливість (а особливо важких випадках вони можуть взагалі заклинити). Першу несправність можна усунути, ретельно почистивши гальмівні колодки. А проблема з циліндрами вирішується лише їх заміною (ремонту ці пристрої не підлягають). Тут слід відзначити ще один момент: машина може погано гальмувати і через те, що гальма просто перегрілися. Це відбувається при їзді поганою дорогою в сильну спеку. Тут вихід тільки один - зупинитися і дати гальмам охолонути;
Передні гальмівні колодки ВАЗ 2106 іноді приходять у повну непридатність через забруднення.
у педалі гальма зник вільний хід. Ця несправність зазвичай виникає не через витік гальмівної рідини, а через погане регулювання педалі. Згодом її кріплення слабшає і педаль починає бовтатися. Рішення очевидне - встановити педаль у правильне положення, попередньо зазирнувши в інструкцію з експлуатації машини;
Щоб правильно виставити гальмівну педаль, доведеться заглянути в інструкцію
одне з коліс постійно гальмує при відпущеній гальмівній педалі. Найчастіше це відбувається із задніми колесами, коли слабшає або обривається пружина, що повертає колодки у вихідний стан після зняття машини з ручника. Для вирішення проблеми пружину доведеться поміняти. А якщо мимоволі почало гальмувати переднє колесо, то проблема криється в поршні, який просто перестав своєчасно висуватися зі свого циліндра через іржу або бруд. Залежно від ступеня пошкоджень, цей поршень доведеться або ретельно очистити, або замінити разом з гідравлічним циліндром;
Через ослаблення пружини задніх колодок колесо починає мимоволі гальмувати
при гальмуванні машину сильно тягне убік (або вона взагалі входить у замет). Причин цього явища може бути кілька. Або зламався один з робочих циліндрів у супорті, або одна з гальмівних трубок виявилася погнутою, внаслідок чого гальмівна рідина не доходить до циліндра. Обидві проблеми вирішуються заміною зламаних деталей. Тут слід зазначити, що вищезгадана несправність може бути пов'язана не тільки з системою гальмування, але і з різним тиском в шинах. Тому перш ніж розбирати гальма, слід ретельно оглянути колеса: можливо, одне з них злегка спустило;
Іноді машину веде убік не через гальма, а через спущене колесо.
гальмівна педаль важко натискається. Це відбувається при поломці вакуумного підсилювача. Для усунення проблеми підсилювач доведеться замінити. Ця деталь не підлягає ремонту, тому що знайти у продажу запасні частини до неї неможливо, та й відкрити корпус підсилювача без його поломки не вдасться;
биття гальмівної педалі. Вібрація на педалі виникає, коли гальмівний диск сильно зношений. Тут же слід сказати, що биття можуть з'явитися і через зношені колодки, але через пошкодження диска вони виникають частіше, оскільки диск з часом покривається невеликими заглибленнями і борознами. При спробі здавити такий диск плоскими колодками починається вібрація, яка спочатку переходить на підвіску, а потім і на педаль гальма. Щоб позбавитися її, доведеться поміняти гальмівний диск разом з колодками (у таких ситуаціях вони теж бувають сильно пошкоджені).
високий тиск. Мінімальний тиск, який має витримувати гальмівний шланг ВАЗ 2106, становить 200 бар. При такому навантаженні не повинно виникати жодних витоків;
розрив. Шланги розтягуються з тиском 1200 бар. Якісний виріб при цьому не має рватися;
вигин та об'ємне розширення.
Спочатку перевіряється рівень гальмівної рідини. Бачок має бути заповнений до верхніх позначок.
Після цього помічник, що сидить у кабіні, повинен двічі-тричі натиснути на гальма, а потім потримати педаль натиснутою протягом однієї хвилини.
У цей момент штуцер відкручується так, щоб із нього через шланг полилася гальмівна рідина. У ній будуть видні бульбашки повітря.
Через деякий час педаль гальма остаточно провалиться в підлогу, про що повідомляє помічник. Як тільки це станеться, слід затягнути штуцер і повторити всі перераховані вище дії. Робити це необхідно доти, поки зі шланга не перестане текти рідина з бульбашками.
Коли гальмівна рідина, що витікає, стане нормальною, процедуру прокачування слід виконати з іншими колесами.
- плакати по темі уроку;
планшет з інструментами;
- комп’ютер, телевізор.
Міжпредметні зв’язки: «Спецтехнологія», «Слюсарна справа», «Охорона праці».
Література: Лудченко О. Л. "Технічне обслуговування і ремонт автомобілів: організація і управління: Підручник"
ХІД УРОКУ
І. Організаційна частина (– 5хв).
- привітання.
- перевірка наявності здобувачів освіти.
- перевірка готовності здобувачів освіти до уроку.
- дотримання правил з охорони праці.
ІІ. Вступний інструктаж (– 40хв)
1. Який з перерахованих шарнірів є шарніром нерівних кутових швидкостей?
а) шарнір, що складається з вилок, куркулів і диска
+ б) шарнір, що складається з фасонних кулаків і кульок
в) шарнір, що складається з двох вилок і хрестовини
2. Куди передається крутний момент карданної передачею?
+ а) від коробки передач до ведучого моста
б) від коробки передач до роздавальної коробці
в) від коробки передач до неведучого мосту
3. Чи змінює карданна передача величину крутного моменту?
+ а) не змінює
б) зменшує крутний момент
в) збільшує крутний момент
4. Для чого призначена карданна передача?
а) для збільшення крутного моменту
+ б) для передачі крутного моменту під кутом
в) для плавної роботи ведучого моста
г) для гасіння вібрацій, що передаються від дороги на кузов
5. Максимальний кут нахилу валів:
+ а) 25°;
б) 45°;
в) 35°;
г) 55°.
6. Карданні шарніри по кінематиці:
а) осьові;
б) швидкохідні;
в) дезаксіальні;
г) рівних кутових швидкостей (синхронні);
+ д) нерівних кутових швидкостей (асинхронні)

Пояснення нового матеріалу.
Порядок і техніка ремонту карданної передачі
Для усунення несправностей в деталях карданну передачу знімають з автомобіля і розбирають на стенді. Перед розбиранням рекомендується маркувати деталі мітками для збереження при складанні початкового їх положення. Основними дефектами деталей карданної передачі є знос шийок, підшипників, сальників хрестовини, отворів в валиках, шліців на валах і качанах, прогин або скручування валів, знос опорного підшипника проміжного вала.
Зношені шийки хрестовини відновлюють хромуванням. Сальники і зношені підшипники замінюють новими. Не можна експлуатувати голчасті підшипники, в яких не вистачає хоча б одного ролика. Якщо на шиях хрестовини є вм'ятини від роликів, то слід замінити хрестовину в зборі з підшипниками.
ковзаючі вилки карданних шарнірів зі зношеними шлицами зазвичай заміняють новими. Вилка зі зношеними шлицами по зовнішньому діаметру і по товщині може бути відновлена ??наплавленням, застосовуючи постійний струм зворотної полярності. Після наплавлення здійснюють нормалізацію при температурі нагріву 860 ° С, механічну обробку (проточку і нарізування шліц), загартування, відпустка і шліфування по зовнішньому діаметру. Ковзаючі вилки повинні вільно, без заїдання, переміщатися уздовж шліцьовій частини карданного валу. При цьому не повинно бути відчутного радіального люфту.
Перевірку карданних валів на биття виробляють індикатором при установці їх на призми. Биття в будь-якій точці по довжині труби не повинно перевищувати значень, встановлених технічними умовами. Вали, що мають скручування, знос і зминання шліців, замінять новими. При складанні карданної передачі вилки карданних шарнірів повинні розташовуватися в одній площині. Карданний вал заднього моста і проміжний вал повинні піддаватися динамічному балансуванню на стенді. Дисбаланс не повинен перевищувати зазначеного в технічних умовах значення.

Труби карданних валів виготовляють зі сталей 15...20, НВ 80.. .100, а вилки - зі сталей 35 і 40, НВ 170 ... 235.
Дефекти карданного вала
Позиції на рис.
|
Дефекти |
Розміри, допустимі без ремонту, мм |
1 |
Скручування труби вала |
— |
2 |
Знос отворів у вильці під підшипники |
39,050 |
3 |
Зміна розміру (погнутість) між щоками вилки |
118,050 |
4 |
Погнутість вала |
— |
Скручування труби вала більше 3° вимагає її заміни. Скручування труби визначається виміром взаємного кутового положення осей поверхні Б вилок. Приварювання нової труби до вилок виконується під шаром флюсу; допускається приварювання і у середовищі вуглекислого газу.
Погнутість вала визначають після його установки в пристосування по поверхнях Б та В, при цьому його радіальне биття в перерізі А - А повинне бути не більше 0,40 мм, а на всій довжині труби не більше 0,80 мм. При більших значеннях радіального биття вал правлять на пресі; при неможливості усунути дефект, трубу заміняють. Зміну розміру між щоками вилки усувають виправленням. При неможливості усунути дефект даним способом - вилку заміняють. При зношуванні отвору у вилці під підшипник її заміняють.
Відновлений карданний вал повинен відповідати наступним технічним вимогам:
Хрестовини карданних валів виготовляють в автомобілів ЗІЛ зі сталі 55, HRC 60...65, у ГАЗ - зі сталі 20Х, HRC 60 і менше, у МАЗ - зі сталі 18ХГТ, HRC 58... 64.
Мал. Основні дефекти хрестовини карданних валів автомобілів ЗІЛ
Дефекти хрестовини карданних валів
Позиції на рис.13.8 |
Дефекти |
Розміри, допустимі без ремонту, мм |
1 |
Знос торців шипів |
107,850 |
2 |
Знос шипів по діаметру |
24,950 |
Зношування торців шипів визначається виміром відстані між ними. При розмірі менше допустимого хрестовина бракується.
Зношування шипів по діаметру усувають наплавленням їх у середовищі вуглекислого газу з наступним шліфуванням під розмір робочого креслення.
Відновлена хрестовина карданних валів повинна відповідати наступним технічним вимогам:
- по поверхнях А: не циліндричність (на довжині 20,0 мм від поверхні Б) не більше 0,007 мм, відхилення осей від положення в одній площині не більше 0,3 мм, неперпендикулярність осей не більше 0,2 мм;
Показ прийомів роботи майстром виробничого навчання.
Перед початком роботи майстер в/н показує здобувачам освіти:
- організацію робочого місця;
- обладнання, інструмент, пристосування;
- способи виконання робіт;
- технічні умови і вказівки щодо виконання завдання;
- правила з охорони праці .
ІНСТРУКЦІЙНО - ТЕХНОЛОГІЧНА КАРТКА
ТЕМА: Розбирання, ремонт, складання та випробування карданної передачі.
№ п/п |
Операція |
Технологічна послідовність виконання робіт |
Ескізи |
Інструменти та обладнання |
Технічні умови |
1 |
Зняття стопорних пружинних кілець |
Легкими ударами молотка через мідну або алюмінієву оправку постукайте по дну кожного кільця (склянки) підшипників і зніміть за допомогою викрутки стопорні пружинні кільця 22.
|
|
Молоток
Викрутка |
|
2 |
Випресуваня підшипників |
Встановіть карданний шарнір в пристосування ( мал. ) так, щоб нижня провушина вилки 3 спиралася на упор 1, і за допомогою преса, натискаючи через скобу 4 і хрестовину шарніра, випресуйте підшипник з нижнього вушка. Потім поверніть шарнір на 180 градусів, вставте його знову в пристосування і таким же способом випресуйте другий підшипник тієї ж вилки.
|
|
Струбцина (знічач)
або оправка
з молотком для
випресовування та
запресовування
голчатих підшипників;
|
|
3 |
Роз’єднання вилки карданного шарніра |
Роз'єднаєте вилки карданного шарніра.
|
|
|
|
4 |
Випрасовування підшипників |
Надіньте роликові підшипники на вільні кінці хрестовини, щоб не пошкодити їх, вставте вилку в пристосування так, щоб її нижня проушина спиралася на упори 1, і за допомогою преса, натискаючи через скобу 4 і кільця підшипників на хрестовину, випресуйте нижній, а потім верхній підшипники . |
|
Прес |
|
5 |
Зняття сальників |
При необхідності зніміть з хрестовини гумові сальники 24 |
|
|
|
6 |
Промивання шипів і отворів хрестовини |
Промийте шипи і наскрізні отвори хрестовини, попередньо вивернувши запобіжний клапан 17 і пробку 18. |
|
Пензлик
Посуд Керосин |
|
7 |
Усунення погнутості вала |
Відновлюють вал правкою на пресі |
|
Прес
|
|
8 |
Усунення зміненого розміру між щоками вилки |
Змінений розмір між щоками вилки усувають правкою |
|
|
|
9 |
Приварювання нової труби до вилки |
Приварюють під флюсом. Допускається приварювання вуглекислим газом |
|
Зварювальний
апарат |
|
10 |
Усування зносу шипів по діаметру |
Знос шипів по діаметру усуваємо наплавкою іх в середовище вуглекислого газу з послідуючим шліфуванням під розмір робочого креслення |
|
Шліфувальний
верстат |
|
5. Закріплення нового матеріалу
Закріплення проводиться шляхом фронтального опитування з питань:
Розподіл здобувачів освіти за робочими місцями, повідомлення про критерії оцінювання виконуваних робіт.
ІІІ. Поточний інструктаж. (5год.)
- Видання завдань для самостійної роботи здобувачів освіти.
- Цільові обходи майстра виробничого навчання робочих місць здобувачів освіти:
1 обхід – перевірити організацію робочих місць.
2 обхід – допомога окремим здобувачам освіти в організації робочого місця та виконанні завдань.
3 обхід – перевірити чи всі здобувачі освіти дотримуються правил охорони праці.
4 обхід – індивідуальна допомога здобувачам освіти в виконанні завдань.
5 обхід – перевірити правильність виконання робіт.
6 обхід – допомога окремим здобувачам освіти в виконанні робіт, дотримання технологічного процесу.
7обхід- додаткове інструктування в випадку неправильного виконання робіт
8 обхід – прийом і оцінювання виконаних робіт.
- Прибирання робочих місць, інструменту.
ІV. Заключний інструктаж
оголошення оцінок.
![]() |
СРКТЗ-3.2 « Виконання ремонту вантажних автомобілів в т.ч. спеціальних, газобалонних та дизельних ,легкових автомобілів, мікроавтобусів і автобусів ». |
ПЛАН УРОКУ 17
Спеціальність: «Слюсар з ремонту колісних транспортних засобів»
Тема програми: СРКТЗ-3.2 « Виконання ремонту вантажних автомобілів в т.ч. спеціальних, газобалонних та дизельних ,легкових автомобілів, мікроавтобусів і автобусів ».
Тема уроку: « Розбирання та складання робочих гальмівних циліндрів.
Мета уроку:
навчальна: навчити здобувачів освіти володіння прийомам ремонту робочих гальмівних циліндрів, користування необхідним інструментом при відпрацьовуванні прийомів робіт з дотримання вимог ОП;
виховна: звернути увагу на раціональне використання матеріалів, економне використання енергоресурсів, бережне ставлення до обладнання та інструменту, формувати культуру виробничої діяльності;
розвивальна: формувати самостійність при виконанні робіт, сприяти розвитку технічного мислення та культури праці.
Тип уроку: Урок формування вмінь та навичок.
Вид уроку: Виконання вправ.
Матеріально – технічне забезпечення:
- інструкційно - технологічні картки;
- презентація;
- плакати по темі уроку;
- планшет з інструментами;
- компютер.
Міжпредметні зв’язки: «Спецтехнологія», «Слюсарна справа», «Охорона праці».
Література: Лудченко О. Л. "Технічне обслуговування і ремонт автомобілів”
ХІД УРОКУ
І. Організаційна частина (– 5хв).
- привітання.
- перевірка наявності здобувачів освіти.
- перевірка готовності здобувачів освіти до уроку.
- дотримання правил з охорони праці.
ІІ. Вступний інструктаж (– 40хв)
1. Будова гідравлічної гальмівної системи автомобіля.
2. Будова головного циліндра гідравлічної гальмівної системи автомобіля.
3. Будова робочого циліндра гідравлічної гальмівної системи автомобіля.
- Пояснення нового матеріалу.
Головні несправності гальмової системи з пневматичним, гідравлічним та комбінованим приводами.
Основними несправностями робочих гальмівних систем можуть бути слабка або неодночасна дія гальм, погане розгальмовування або заклинювання колодок гальмівних механізмів коліс. Слабка дія гальм виявляється за збільшенням гальмівного шляху. Для автомобіля ГАЗ-3307 без навантаження при гальмуванні з швидкості 30 км/год., на сухій горизонтальній ділянці дорогі з твердим покриттям гальмівний шлях не повинен перевищувати 9,5 м, а для автомобіля ЗИЛ-130 в цих же умовах — 11 м. Гальмівний слід від правих і лівих коліс повинен бути однакової довжини. Причиною слабкої дії гальм може бути негерметичність гальмівного приводу, попадання повітря в систему гідравлічного приводу або недостатню кількість гальмівної рідини, порушення регулювання приводу або гальмівних механізмів, знос або замаслення гальмівних колодок і барабанів, недостатня кількість стислого повітря в пневматичному приводі із-за його витоку або несправності компресора. Неодночасність дії гальм виявляється по занесенню автомобіля убік при гальмуванні. Причиною цього може бути порушення регулювання гальмівних механізмів, засмічення трубопроводів або замаслення окремих колодок. Несправність усувається регулюванням гальмівних механізмів, промивкою намаслених колодок, очищенням трубопроводів, що засмітилися.
Погане розгальмовування або заклинювання коліс відбувається унаслідок поломки відтяжних пружин, обриву фрикційних накладок, заїдання валів розтискних кулаків, несправності гальмівного крана, недостатнього вільного ходу гальмівної педалі, розбухання манжет або заклинювання поршнів колісних циліндрів, засмічення компенсаційного отвору в головному гальмівному циліндрі.
Залежно від несправності проводяться: заміна поламаних пружин, обірваних накладок, регулювання вільного ходу педалі, заміна манжет колісних циліндрів, очищення головного циліндра, ремонт гальмівного крана.
Основною несправністю гальмівної системи стоянки може бути погане утримання автомобіля на місці. Ця несправність виникає унаслідок великого зазору між колодками барабаном (усувається регулюванням гальма) або із-за заїдання або корозії в розтискному пристрої (усувається розбірною, промивкою і змащеннями деталей).
Перевірка герметичності з'єднань пневматичного, гідравлічного та комбінованого приводів гальм.
Негерметичність гідравлічного приводу визначається по підтіканню рідини в з'єднаннях, негерметичність пневматичного приводу виявляється по падінню тиску повітря в системі при непрацюючому двигуні. Витік виявляється на слух або за допомогою мильного розчину. При вільному положенні педалі і непрацюючому двигуні падіння тиску в пневматичній системі повинне бути не більше 50 кПа (0,5 кгс/см2 ) за 30 хв. Негерметичність приводів усувається підтяганням з'єднань, заміною поламаних або зношених деталей.
Регулювання тиску повітря в пневматичнім приводі гальмової системи При малому тиску, що розвивається компресором, перевіряють натягнення ременя його приводу і роботу регулятора тиску (Рисунок 10.1).
Регулятор регулюється таким чином. Обертанням ковпака 3 добиваються, щоб компресор включався в роботу при тиску 600—640 кПа (6,0—6,4 кгс/см2 ). Зміною кількості прокладок між сідлами впускного і випускного клапанів встановлюють тиск 730—770 кПа (7,3—7,7 кгс/см2 ), при якому компресор відключається. Розкривати і регулювати регулятор дозволяється тільки кваліфікованим фахівцям.
Натягнення ременя приводу компресора регулюють переміщенням самого компресора щодо опорного кронштейна за допомогою регулювального болта. Заздалегідь потрібно ослабити гайки кріплення нижньої кришки до опорного кронштейна. Ремінь повинен бути натягнутий так, щоб його прогинання в середині гілки від зусилля 4 кгс було 5—8 мм.
Регулювання колісних гальмових механізмів з пневматичним та гідравлічним приводами Гальмівні механізми мають два регулювання — часткову і повну.
Часткове регулювання проводиться для відновлення нормального зазору між колодками і барабаном.
При виконанні цього регулювання необхідно:
- підняти колесо домкратом;
- обертаючи колесо вперед, злегка повернути ексцентрик передньої колодки, поки колодка не загальмує колесо;
- поступово відпустити ексцентрик, повертаючи колесо від руки до тих пір, поки колесо не стане обертатися вільно;
- при регулюванні передньої колодки заднього гальма колесо треба обертати вперед, а при регулюванні задньої колодки заднього гальма — назад;
- виконати регулювання решти гальмівних механізмів;
- перевірити, чи не нагріваються гальмівні барабани на ходу автомобіля.
При правильно відрегульованих зазорах між колодками і барабанами гальмівна педаль при повному гальмуванні повинна спускатися не більше ніж на половину ходу. Повне регулювання виконується після зміни колодок або накладок. Її мета — правильна установка колодок щодо барабана. Опорні пальці встановлюються в початкове положення. При натисненні на педаль з силою 85 120—160 Н (12—16 кгс) опорні пальці повертаються так, щоб нижня частина накладки стосувалася гальмівного барабана. Момент, коли це відбувається, визначається по збільшенню опору повороту опорного пальця. У цьому положенні слід зафіксувати пальці гайками і повернути регулювальні ексцентрики так, щоб колодки стосувалися барабана. Припинивши натиснення на педаль, потрібно повернути ексцентрики у зворотному напрямі до вільного обертання колеса.
Рисунок 10.1 - Регулятор тиску [4]: 1 - кожух ; 2 - пружина регулятора ; 3 - завзятий кульку ; 4 - регулювальний ковпак ; 5 - шток клапанів ; 6 - штуцер ; 7 - сітчастий фільтр ; 8 - фільтр ; 9 - кільце ущільнювача ; 10- корпус регулятора тиску; 11 -пробка фільтра ; 12 - пружина клапана ; 13 - впускний клапан ; 14 - випускний клапан ; 15 - регулювальні прокладки ; 16 - контргайка регулювального ковпака ; А - впускний отвір ; Б - отвір, що з'єднує внутрішню порожнину регулятора з атмосферою ; В - отвір , провідне до фільтру.
Регулювання вільного ходу педалі пневматичного, гідравлічного та комбінованого приводу гальмової системи
Вільний хід педалі гальма повинен бути 40 — 60 мм, верхній кінець педалі не повинен доходити до підлоги на 10 — 30 мм. Вільний хід педалі регулюється зміною довжини тяги, що сполучає педаль гальма з гальмівним краном, шляхом нагвинчування або згвинчування її вилки. Регулювання тиску повітря в сполучній магістралі причепа здійснюється обертанням направляючої штока верхньої секції крана при знятому корпусі важелів і ослабленій контргайці направляючої. Тиск в сполучній магістралі причепа повинен бути при відпущеній педалі гальма 480 — 530 кПа (4,8—5,3 кгс/см2 ). Перевіряється тиск приєднанням манометра до сполучної головки.
Усунення повітря із системи гідравлічного приводу гальм
Наявність повітря в гідравлічному приводі визначається по натисненню на педаль. Якщо педаль опускається без опору (провалюється), то це означає, що в приводі є повітря. За наявності повітря в системі його слід видалити прокачуванням системи (Рисунок 10.2). Перед цим перевіряється рівень рідини в головному циліндрі. Рівень повинен бути нижче за верхній край холодцю отворами на 15—20 мм.
Рисунок 10.2 - Прокачування гідравлічного приводу гальм [5].
Гідравлічний привід прокачують удвох. Одна людина на колісному циліндрі знімає ковпачок з перепускного клапана, приєднує до нього гумовий шланг завдовжки 350—400 мм, опускає шланг в скляну банку, наповнену на 1/3 гальмівною рідиною, і відкриває на 1/2—3/4 обороту перепускний клапан (Рисунок 10.2). Після цього напарник кілька разів швидко натискає на гальмівну педаль і поволі відпускає її. Прокачування продовжується до тих пір, поки з трубки, опущеної в банку, не перестануть з'являтися бульбашки повітря. Через кожних 5—6 натиснень на педаль слід перевіряти рівень рідини в головному циліндрі або бачку і своєчасно туди її доливати. Коли бульбашки повітря вже не з'являються, не відпускаючи педалі, щільно загорнути перепускний клапан колісного циліндра, зняти шланг і надіти на клапан ковпачок. Після прокачування довести рівень рідини в головному циліндрі до норми.
Прокачування гальмівної системи можливо провести самостійно, однак для цього необхідно підготувати спеціальні засоби, зокрема: автомобільну камеру, шланг, кришку зі штуцером, що підходить по діаметру до заливного бачка гальмівної системи. Процес прокачування починаємо з накачування камери стисненим повітрям, під’єднанням до неї шланга, в той же момент надіваємо шланг на кришку зі штуцером, бачок гальмівної системи повинен бути заповнений гальмівною рідиною повністю. Після проведення підготовчих робіт починаємо прокачування аналогічно до вище описаної технології.
Регулювання механічного стоянкового гальма
Регулювання стоянкового гальма (Рисунок 10.3) проводиться зміною довжини тяги 16 і важелем 12. Спочатку гальмо регулюють тягою 16. При цьому тягу від'єднують від важеля 18, ставлять цей важіль в крайнє нижнє положення до упору і, змінюючи довжину тяги 16 різьбовою вилкою 17, 87 добиваються такого положення, щоб після приєднання тяги до важеля 18 повне загальмовування відбувалося при переміщенні стопорної клямки 20 на 2 — 6 зуба зубчатого сектора. Якщо укорочена до межі тяга не забезпечує регулювання гальма, то палець, до якого приєднується кінець штанги 13, переставляється на черговий отвір сектора і повторюється регулювання тягою 16.7
10.3 - Гальмівна стоянкова система автомобіля ЗИЛ-131: 1 — роздавальна коробка; 2 — гальмівна колодка з фрикційною накладкою; 3 — щиток; 4 — вісь колодок; 5, 8 — пружини; 6 — опорний кронштейн; 7 — фланець вторинного валу; 9 — розтискний кулак; 10 — сухар колодки; 11 — сальник; 12 — регулювальний важіль; 13 — штанга; 14 — кутовий важіль; 16 — кронштейн кутового важеля; 16 — тяга приводу; 17 — вилка тяги; 18 — важіль гальма; 19 — зубчатий сектор важеля приводу; 20 — стопорна клямка; 21 — тяга приводу гальмівного крана; 22 — тяга клямки; 23 — рукоятка важеля; 24 — рукоятка тяги клямки; 25 — гальмівний барабан.
Технічне обслуговування.
Через кожні 10 тис. км пробігу автомобіля перевірити рівень гальмівної рідини в живильних бачках; доливати її до нижньої кромки заливної горловини (на автомобілі ВАЗ – до рівня 30…32 мм нижче від верхнього краю горловини). Підтягнути кріплення супортів гальм передніх коліс на автомобілях ВАЗ та «Москвич - 2140» і перевірити стан накладок гальмівних колодок дискових гальм. У разі спрацювання до товщини 1,5 мм колодки треба замінити. Диск підлягає заміні в разі спрацювання до товщини менш ніж 10 мм.
Через кожні 20 тис. км пробігу автомобіля перевіряють стан гальм барабанного типу. Їхні колодки підлягають заміні, якщо виявлено поломки й деформації, які знижують ефективність гальмування, а також у разі спрацювання накладок до товщини 2 мм. Перевірити також хід важеля стоянкового гальма (перша перевірка – після 2…3 тис. км пробігу нового автомобіля).
Через 30 тис. км пробігу автомобіля перевірити працездатність вакуумного підсилювача гальмового привода (Рисунок 10.4). Для цього, вимкнувши двигун, натискають на педаль гальма 5 – 6 разів і, залишивши її натиснутою приблизно на половині ходу, ввімкнути двигун. Якщо підсилювач справний, педаль після пуску двигуна має піти «вперед». У противному разі слід перевірити герметичність приєднання шланга до впускної труби двигуна та до підсилювача й, щоб запобігти можливому підсмоктування повітря, підтягнути з’єднання.
Рисунок 10.4 - Пневмопідсилювач гальм автомобілів ВАЗ 2170 2171 2172 Лада Приора (Lada Priora): 1 фланець кріплення наконечника; 2 шток; 3 зворотна пружина діафрагми; 4 ущільнююче кільце фланця головного циліндра; 4 головний гальмівний циліндр; 5 шпилька підсилювача; 6 корпус підсилювача; 7 діафрагма; 8 кришка корпуса підсилювача; 9 поршень; 10 захисний чохол корпуса клапана; 11 штовхач; 12 зворотна пружина штовхача; 13 пружина клапана; 14 слідкуючий клапан; 15 буфер штока; 16 корпус клапана; А – вакуумна камера; В – атмосферна камера; С, D – канали [7]. Також слід через кожні 65 – 75 тисяч кілометрів пробігу (залежно від моделі автомобіля) або 4 роки експлуатації замінити гальмівну рідину у системі гідроприводу гальм. Гальмівні гумові шланги слід замінити через 125 тисяч кілометрів пробігу або 5 років експлуатації.
Схеми прокачування гальмівних систем автомобілів.
Робочий контур, відповідно до вимог ЄЕС, повинен ділитися на основний і допоміжний. Якщо вся система справна, то працюють обидва, але при розгерметизації одного - інший продовжує працювати, стаючи допоміжним (аварійним). Найбільш поширені три компоновки розділення робочих контурів (Рисунок 10.5) : - 2 + 2 гальмівних механізми, підключених паралельно (передні + задні); - 2 + 2 гальмівних механізму, підключених діагонально (правий передній + лівий задній і т. Д.); - 4 + 2 гальмівних механізму (в один контур підключені гальмівні механізми всіх коліс, а в іншій тільки два передніх). А) Б) В) Рисунок 10.5 - Схеми компонування гідропривода гальмівної системи автомобілів: (А-Б) - паралельне підключення; В - діагональне підключення.
Необхідно відзначити, що на багатьох імпортних машинах в гальмівний привід вбудовують антиблокувальні системи "колісних" гальмівних механізмів, які в недалекому майбутньому стануть обов'язковим атрибутом автомобіля. У Європі вже введена в законодавчому порядку установка АБС на міжміських автобусах і важких автомобілях. Конструктивно АБС являє собою сукупність датчиків, модуляторів і блоку управління.
При гальмуванні блок управління аналізує сигнал, що надходить від датчиків, а саме інформацію про реальну швидкість автомобіля і кутову швидкість обертання коліс, відстежує роботу модуляторів (виконавчих механізмів), які регулюють тиск рідини в тому чи іншому колісному гальмівному механізмі, не даючи йому заблокуватися в разі екстреного гальмування.
Таким чином, для будь-якого стану дорожнього покриття визначається режим "відносного ковзання", що забезпечує мінімальний гальмівний шлях, і повне блокування коліс стає неможливою при будь-якому зусиллі на гальмівну педаль.
Контрольні запитання
1. Назвіть головні несправності гальмової системи з пневматичним, гідравлічним та комбінованим приводами?
2. Як провести перевірку герметичності з'єднань пневматичного, гідравлічного та комбінованого приводів гальм.
3. Опишіть процес регулювання тиску повітря в пневматичнім приводі гальмової системи.
4. Як проводять регулювання колісних гальмових механізмів з пневматичним та гідравлічним приводами
5. Опишіть процес регулювання вільного ходу педалі пневматичного, гідравлічного та комбінованого приводу гальмової системи.
6. Як проводиться процес усунення повітря із системи гідравлічного приводу гальм?
7. Як проводиться процес регулювання системи механічного стоянкового гальма?
8. Назвіть основні несправності гальм з пневмоприводом і їх ознаки?
9. Які можуть бути причини повного відказу гальм?
10. Назвіть основні операції ЩО, ТО – 1, ТО- 2 і СО гальмових систем з пневмо і гідроприводом?
Практично на всіх ВАЗах встановлювалась однакова система гальмування, тому можна розглянути гальмівну систему автомобіля ВАЗ на прикладі ВАЗ 2106, в народі іменується як «шістка». Автомобіль містить дві гальмівні системи: робочу і стояночную. Робоча система зупиняє автомобіль під час його руху, а стоянкова не допускає довільного руху автомобіля під час стоянки. Робоче гальмо працює за коштами гідравліки, а гальмо має механічний привід.
Робоча система гальмування автомобіля ВАЗ має 2 незалежних один від одного контуру, які забезпечують окрему гальмування передніх і задніх коліс. Робоча система приводиться в дію педаллю гальма. Вся гідравлічна система складається з головного гальмового циліндра, вакуумного підсилювача, барильця головного гальма, регулятора задніх гальм і механізмів гальмування задніх і передніх коліс.
Прокачувати
гальмівну систему найзручніше з
напарником. Напарник домагається тугого
натискання педалі гальма шляхом
багатократних натискань. Потім фіксує
її в натиснутому положенні, після цього
Ви откручиваете штуцер на колісному
циліндрі і спускаєте частина гальмівної
рідини разом з повітрям. Педаль повинна
провалити до самої підлоги, але відпускати
її потрібно тільки після закручування
штуцера. Такі дії повторити кілька разів
на кожному колесі.
Якщо ж у Вас немає
напарника, то гальмівну систему автомобіля
ВАЗ можна прокачати самостійно. Для
цього вам знадобиться кришка з алюмінію
для головного гальмівного циліндра. У
неї потрібно закрутити вентиль від
камери і з’єднати шлангочкой з запаскою
(дав. 0.05-0.08 МПа). Ось і весь спосіб.

Гальмівна педаль повинна мати не великий вільний хід, приблизно 4-6мм. Дуже маленький вільний хід говорить про те, що колісний циліндр заїдає. Це призведе до швидкого зносу гальмівних колодок і підвищує витрату пального. Дуже великий хід говорить про те, що збільшені допустимі інтервали в механізмі педалі. Або ж про те, що гальмівна система не герметична. Якщо, часто натискаючи на гальма, хід педалі зменшується, значить в систему потрапило повітря. Усунути його можна прокачування.
Якщо педаль вібрує при гальмуванні, то можливо це зносилися гальмівні диски. У цьому випадку їх доведеться замінити на нові. При чому міняти потрібно одночасно два диска.
Типові ознаки поломки гальм ВАЗ 2106
Система гальмування – найважливіша частина автомобіля. Саме від її справності залежить не лише безпека, а й життя водія. Тому за станом гальм власнику ВАЗ 2106 слід стежити особливо ретельно. Перелічимо найпоширеніші поломки в системах гальмування «шісток»:

Гальмівний диск з часом покривається борознами та поглибленнями та стає причиною появи вібрацій на гальмівній педалі.
Розглянемо особливості пристрою та роботи всіх основних деталей, що забезпечують гальмування автомобіля.
Основний гальмівний циліндр
Система гальмування на ВАЗ 2106 розбита на два контури: первинний та вторинний. Це зроблено для того, щоб при поломці передніх гальм водій міг скористатися задніми і навпаки. І первинний, і вторинний контури обладнані гідравлічними циліндрами, що висувають поршні з колодок. А тиск у всій системі створюється головним циліндром. Після початку гальмування поршень у цьому циліндрі починає переміщатися, нагнітаючи рідину у первинний контур (або у вторинний — все залежить від того, якими гальмами скористався водій).
Головний гальмівний циліндр створює тиск рідини у всій гальмівній системі
Рідина через шланги доходить до гідравлічних циліндрів, з яких висуваються поршні, що натискають на колодки. Взагалі, в основному циліндрі «шістки» є не один, а два потужні поршні, поміщені в спеціальні ущільнювальні контейнери. Основний поршень з'єднаний з головною штангою педалі гальма, а додатковий підключений до основного і починає рухатися за ним. Коли потреба у гальмуванні відпадає, водій прибирає ногу з гальмівної педалі. Після цього в справу вступають поворотні пружини, які прибирають поршні, що змістилися на вихідні позиції до наступного гальмування.
Під капотом ВАЗ 2106 знаходяться бачок, вакуумний підсилювач та головний циліндр, зібрані в єдину систему.
Якщо відкрити капот ВАЗ 2106, основний циліндр гальм можна побачити під вакуумним підсилювачем, з яким він становить єдину систему. А ще поруч із цим циліндром розташовується невеликий бачок, розділений перегородкою на дві нерівні половини. У цьому бачку зберігається невеликий резерв гальмівної рідини. Якщо в якомусь контурі почнеться витік, деякий час рідина надходитиме в систему з цього бачка, заповнюючи втрати. Якщо запас рідини вичерпається до того, як витік буде знайдений і усунений, гальма відмовить і водій опиниться в смертельній небезпеці.
вакуумний підсилювач
Вакуумний підсилювач є проміжною ланкою між педаллю та основним циліндром гальм. Як тільки натискається гальмівна педаль, її тиск через кілька невеликих важелів досягає вакуумного підсилювача. Цей пристрій є герметичний корпус, розділений на дві половинки еластичною мембраною.
Вакуумний підсилювач є простим корпусом з діафрагмою всередині
До однієї половинки підключається патрубок випускного моторного колектора. Коли мотор запускається, тиск у цій половині сильно знижується (причому справжнього, глибокого вакууму там не утворюється, це просто область дуже низького тиску, але в ужитку підсилювач все одно називають вакуумним). Друга половина підсилювальної камери має вихід в атмосферу із нормальним тиском.
Саме вакуумний підсилювач передає зусилля водія на головний гальмівний циліндр.
Коли тиск в одній половині камери дуже низький, а в іншій нормальний, еластична мембрана поступово починає прогинатися туди, де тиск знижений, і тиснути на штовхач. А він викликає усунення поршня в основному гальмівному циліндрі.
Робочі циліндри
Як говорилося вище, робочі гальмівні циліндри повинні з допомогою своїх поршнів викликати зміщення колодок. Циліндри на «шістці», встановлені спереду та ззаду, не сильно відрізняються за конструкцією. Вони складаються з герметичних корпусів із висувними поршнями. Кожен поршень знаходиться в контейнері ущільнювача. Це необхідно для того, щоб унеможливити витік гальмівної рідини під час роботи циліндра.
Передній робочий циліндр ВАЗ 2106 складається з корпусу та поршня, який виходить зі свого контейнера в процесі гальмування.
Різниця між циліндрами спереду та ззаду лише у схемі докладання зусиль. Робочі циліндри в передніх супортах (тих, що з дисками) тиснуть на колодки так, щоб ті зрушувалися і затискали гальмівний диск. А циліндри задніх барабанних гальм тиснуть на С-подібні колодки, щоб ті розсувалися і упиралися у внутрішню стінку барабана.
Задній робочий циліндр тисне на стінки гальмівного барабана зсередини
Гальмівні колодки
Принцип дії гальмівних колодок "шістки" абсолютно однаковий для всіх коліс. Коли колодки працюють, вони просто перетворять один вид енергії на інший. Водій бачить перешкоду, тисне на гальмівну педаль, а колодки стикаються з гальмівним диском або внутрішньою стінкою гальмівного барабана. У місці зіткнення з'являється тертя, яке викликає швидке нагрівання. Тобто кінетична енергія, що виникає при обертанні коліс машини, перетворюється на теплову, гальма, що розігріває. Результатом цього перетворення є зупинка машини.
Передні колодки на ВАЗ 2106 мають плоску форму.
До робочої поверхні колодок кріпиться особливий захисний матеріал, який має підвищений коефіцієнт тертя. А його твердість при цьому значно нижча за твердість гальмівного диска. Щоб отримати такі властивості, виробники використовують різні композитні матеріали, головним наповнювачем яких є тирса м'яких металів, наприклад, міді. На передніх колесах колодки плоскі і здавлюють гальмівний диск зовні. На задніх колесах колодки мають С-подібну форму і впираються в стінки гальмівного барабана зсередини.
Задні колодки на ВАЗ 2106 мають С-подібну форму, що повторює внутрішні контури гальмівного барабана
гальмівні шланги
Гальмівні шланги, поряд з колодками, є найважливішим елементом гальмівної системи ВАЗ 2106. Саме по шлангах гальмівна рідина подається від головного циліндра до робочих гальмових циліндрів. Під час поїздки життя водія «шістки» та його пасажирів у буквальному розумінні залежить від надійності шлангів, тож вимоги до них пред'являються дуже суворі. Гальмівні шланги на "шістці" виконуються тільки з високоякісного каучуку та інструментальної сталі. Вони повинні мати високу зносостійкість, корозійну стійкість і бути несприйнятливими до впливу різних хімічних реактивів, якими посипають дороги в ожеледицю.
До гальмівних шлангів пред'являються найвищі технічні вимоги
Крім того, всі шланги перевіряються на:
Тільки, пройшовши всі ці процедури, деталі встановлюються на автомобіль.
Педаль гальма
Педаль є головним елементом керування гальмівною системою ВАЗ 2106. Вона розташовується під кермовою колонкою, поряд з педалями газу та зчеплення, і використовується як важіль, що дозволяє водію передати м'язове зусилля на головний гальмівний циліндр.
За допомогою педалі водій керує гальмівною системою машини
Правильно відрегульована педаль обов'язково має запас вільного ходу, який становить 4-6 см. Після того, як нога, що натискає на педаль, пройде цю відстань, автомобіль повинен почати плавно гальмувати. Якщо цього не відбувається, значить, є одна з поломок, про які йшлося вище.
Прокачування гальмівної системи ВАЗ 2106
Прокачування гальм проводиться для видалення повітря, що потрапило в гальмівну систему. Визначити наявність повітря просто: педаль гальма спочатку натискається занадто м'яко, а після кількох натискань раптом набуває незвичайної «твердості». Це ознаки повітряної пробки.
Послідовність дій
Спочатку слід сказати, що прокачувати гальма найкраще з помічником. Але при певній вправності це можна зробити і поодинці.
Бачок має бути заповнений рідиною до рівня верхньої кромки пластини кріплення
2. На задньому гальмівному барабані відкручується штуцер, його місце вставляється гумовий шланг, інший кінець шланга опускається у пластикову пляшку.
Штуцер злегка відкручується і до нього вставляється шланг, опущений іншим кінцем у пляшку
Отже, гальмівна система є найважливішою частиною автомобіля. І ставитися до цієї частини слід дуже відповідально. На щастя, гальма на ВАЗ 2106 ніколи не відрізнялися особливою складністю. Головне, що повинен робити автолюбитель-початківець - частіше їх оглядати і перевіряти. І за найменшої підозри на несправність негайно ремонтувати.
Ремонт переднього гальмівного циліндра.
Зніміть із циліндра захисний чохол.
Подавши стиснене повітря через
отвори
для подавання гальмівної
рідини, витягніть
поршень із циліндра.
Акуратно, щоб не пошкодити
дзеркало
циліндра, вийміть кільце
ущільнювача.
За потреби заміни колісного циліндра
або самого клапана виверніть клапан
прокачування.
Уважно огляньте дзеркало
циліндра та робочу поверхню поршня. У
разі виявлення на них слідів зносу,
пошкоджень або сильного корродивання
замініть циліндр і поршень.
Замініть
пошкоджене, розбухле або загублювальну
еластичність кільце ущільнювача.
Рекомендується замінювати кільце під
час кожного розбирання циліндра незалежно
від його стану.
Встановіть у
проточку циліндра нове кільце ущільнювача,
попередньо змазнувши його свіжою
гальмівною рідиною.
Вставте крайку захисного ковпака
у
проточню поршня.
Змащуйте свіжою гальмівною
рідиною
дзеркало циліндра та робочу
поверхню
поршня. Виберіть поршень у
циліндр і встановіть
зовнішню крайку
захисного ковпака
у проточування
корпусу циліндра. Встановіть стопорне
кільце.
18. Встановіть колісний циліндр у
порядку,
зворотному зняттю. Перед
встановленням напрямних
пальців
змащуйте їх мастилом
УНІОЛ-1. Прокачайте
гальмівну систему.
Детальніше: https://prof-shop.com.ua/ua/p1891926045-tsilindr-tormoznoj-rabochij.html